
Author: Eric Vissers, Process technologist at Feed Design Lab.
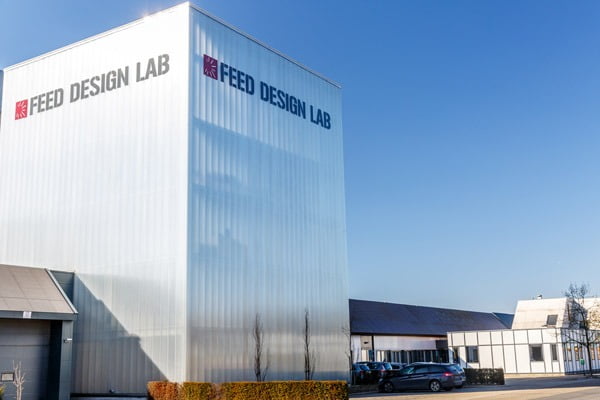
What we must realize is that almost every process step has a certain influence on the subsequent process parts. If we do something deviant somewhere in a process part, this has an influence on the pellet quality. In a some cases positive and in a number of cases also negative.
We’re specifically addressing physical pellet quality here. Nutritional, chemical or microbiological quality will be left out of consideration in this article. Customers often judge the physical quality by the proportion of fines in the end product. Dairy cattle and rabbits in particular can’t handle fines and dust. The customers who feed cattle, including horses, goats, sheep and rabbits, would like to receive rock-hard pellets without any fines or dust, which they regard as good quality. For young, small animals such as broilers and piglets, we would like to feed them with a soft pellet with a high durability. The animal benefits from a soft pellet in view of a not yet fully developed digestive system. The customer, on the other hand, would like a pelleted product with little to no fines or dust. That’s the challenge!
“Hardness and durability are like a lock and key;
They work better when used together!”
We can measure physical pellet quality with a number of parameters:
Hardness: we often measure 10 to 30 pellets. This is necessary because we want to monitor how hard the pellet is for the young and small animals mentioned above. Everyone should realize that a hardness measurement with so few measurements is in some cases not very close to reality. Pellets from the outer rows in a die that is not well worn can increase the hardness considerably. More on the pelleting process later.
Durability: this measurement result is very close to reality and gives a good indication of the physical pellet quality. Using the Holmen tester, you get a beautiful picture of the durability. In other words, how well is the pellet resistant to handling.
Pellet length: for young animals we look closely at the correct pellet length. Especially with horses, we want to produce a nice long pellet without fines and dust (commercial feed).
Dustiness: pig(let) feeds are often dusty. We can overcome the dustiness by spraying a small amount of fat or oil (for example soya-, palm-, coconut-, insect- or salmon oil).
Percentage of fines/dust: this parameter is a good indicator for both pelleted and crumbled products.
The many aspects that influence pellet quality can be classified into several main areas:
- Raw materials
- Composition / recipe
- Machines
- Steam
- Operator
- Miscellaneous
Area 1: Raw materials
In the compound feed industry, we can make the following distinction between raw materials:
o Cereals: this is immediately the group of raw materials from which we expect the most on the journey to good pellet quality. These products are the suppliers of starch. Starch will bring us the pellet quality, in addition to energy for the animal, of course. At the quality control, we are mainly concerned about the physical / nutritional quality such as moisture content and specific weight. Standards are available here to assess quality. We hope for heavy, well-filled pellets with a normal moisture content (11-13%) without weed seed or insects such as corn-weevil, feed enemy number one!
o Derivatives: the meal from soybeans, rapeseed and sunflower seeds mainly provides us with protein and crude fibre (non-starch polysaccharides). Since these products have already undergone a heat treatment, we expect little binding power from them; You can only cook an egg once!
o Minerals: these raw materials have a negative influence on the pellet quality. In most cases, this is not a large proportion of the composition. Especially causing a lot of friction during the pelleting process. This can still result in a hard pellet, but this does not mean a good pellet.
“A hard pellet is not synonymous with a good pellet!”
o Additives: the products are often so small in proportion that they have hardly any influence on the pellet quality. One of the exceptions is the product Lignobond, which is regularly used as a practical pellet binder.
o Liquids: you can divide this group of products into fatty and watery products. The fatty ones have a negative influence on pellet quality. In some cases, they can help the pelleting process, for example with higher proportions of minerals or dairy products. The watery substances such as molasses, alvicol, vinasse can in some cases have a very small positive influence on the pellet quality, especially at a dosing temperature of 35-45⁰C.
Area 2: Composition / recipe
Swine feeds and broiler feeds contain a relatively high proportion of starch in the composition. Good to use for reaching a good pellet quality. Finisher feed products, whereby we feed animals just before slaughter, also contain a significant proportion of fat in the composition. That is actually negative for the pellet quality. Older animals such as sows require a higher proportion of crude fiber. Cattle also do well in compositions with a lot of fiber-rich raw materials. High fiber materials such as palm kernel meal, coconut meal or sunflower seed meal have hardly any binding properties and are therefore often negative for pellet quality. A positive exception is beet pulp, which has a positive influence on the bonds in the pellet within swine feeds. Be aware that excess is harmful! Too much fiber will result in a pellet falling apart after moderate cooling. The fibers then return to their original shape!
Water: only in very few cases the addition of water is positive. Water is often used to increase the moisture content. Hopefully it’s IN the composition/recipe and not on top of the 100%! As an aid for pellet quality, this nutrient has definitely no added value at all.
“Adding water does not make a pellet hard,
the only way of doing this with water is to freeze them!😊“
Area 3: Machines
In the feed industry, the technique partly determines the pellet quality. Factory and machine builders have a lot of knowledge. They often determine what happens in a feed factory.
The knowledge is either at the feed factory, gained from research or based on experience, or at the machine supplier. The following machines play an important role in obtaining pellet quality.
3.1 Hammer mill or other grinding equipment
3.2 Mixer
3.3 Conditioner
3.4 Pre-compactor
3.5 Pellet mill
3.6 Cooler
3.7 Sieve or crumbler
3.8 Coater
3.1 Hammer mill or other grinding equipment
Reducing raw materials to a finer structure is positive for the pellet quality. It is also positive for mixing uniformity and digestion in the animal. A Feed Design Lab visitor once said: “Making feed is very simple; break it, mix it and fix it!”.
Grinding raw materials is a science. Important in this form of raw material particle size reduction are energy consumption, tip speed, product properties, wearing parts, single grinding/composite grinding and air management. In general, the finer the flour, the easier it is to pelletise a hard pellet. Using less energy. The size of the hammer mill with its tip speed also determines the impact force. It makes a big difference in pelletability whether you use broiler feed with a 6 mm sieve in the hammer mill or a 3 mm sieve. A subdivision based on sieve/screen perforation:
a) Aqua feed: sieve 0.5-1.0 mm particles in the extrusion process have to absorb a lot of water, so a lot of surface is desired
b) Pet food: 1.0-1.5 mm: here too an extrusion process with a lot of added process water
c) Cattle feed : 2.0-3.0 mm this has no negative influence on digestion and a positive influence on pellet quality
d) Swine feed: 3.0-4.0 mm: for piglets it is recommended to monitor the structure; too long-standing time of sieves/screens means too fine structure with an increasing pellet hardness but also an increased risk of stomach disorders
e) Broiler feed: 3.0-6.0 mm: 6 mm is chosen for the animal (stimulation of the digestive system), 3 mm is selected for the customer (convenience to pellet quality).
It is recommended for a factory to use a system/management with regard to wearing parts. The replacement of sieves/screens in particular, contributes to a consistent feed quality. Organizing a constantly well-functioning extraction system on a hammermill is also crucial for the grinding result.
Some factories grind several products before storage. In doing so, people are in control of the grinding structure compared to compound/composite grinding. Also positive with regard to energy consumption and grinding behavior of the hammer mill.
Finally, it is also the individual product properties that influence the grinding result. Moisture and fat content, structure, fibres, brittleness, or bendability, etc. all play a role in the grinding process.
“The finer the meal, the harder the pellet”
3.2 Mixer
The mixer, if it is in good condition and used properly, has only a minor influence on the pellet quality. Of course, in the event of a poor mixing degree due to, for example, a too low speed or an incorrect direction of rotation, the pellet mill will react in its behaviour.
3.3 Conditioner (steam mixer)
The most important process step of all! Conditioning is bringing the cold, ground and mixed flour into the right condition to make it into a good pellet. We want to switch from a glass phase to a rubber phase. Or from sandy to kneadable. In a conditioner, a steam mixer, the flour is brought to the desired temperature with the use of a number of paddles in speed rotation and of course steam addition. “Is this steam mixer used with a small or a large filling degree?” At a low filling level, we blow an excess of steam into an empty space. Condensation quickly takes place there. With a 50% filled steam mixer, the flour will have more than an opportunity to absorb the moisture and condensation heat. The simple test to judge the filling degree is as follows: press the emergency stop in full operation, open the mixer, judge the filling degree, take some pictures and please weigh the content in some bucket(s).
Formula: content (kg) x 3600 = retention time (sec)
capacity (kg/h)
If the filling level is (too) low, a few paddles adapting on angle position into counter flow can provide a higher filling level.
The supplier of the mixer can also help with this.
The pre-compacting machine also falls into the conditioning category. There are three ways of pre-compacting, namely expanding, double pellet mill and using a BOA compactor. Important subjects / parameters in the conditioning are moisture, temperature, retention time and pressure.
3.3.1 Moisture
When adding moisture from the steam, saturated dry steam is of crucial importance. With this steam addition, we increase the moisture content by 3 to 4% and we need that exactly to obtain the bonds between particles. If there is an excess of moisture, the (wet) flour will escape between the rolls and the die sooner and the pellet mill will fill up. If the pellet mill continues to produce when wet steam is used, this will be reflected in varying and moderate pellet quality. Added water in a pelleting process is not desirable, moisture from dry steam has a particularly positive effect on pellet quality. In addition, the use of steam has a positive effect on the line capacity. Nowadays flour/meal temperatures of 70 to 80⁰C are used.
“Both the production manager and the quality manager
will be happy by using a lot of steam”
3.3.2 Temperature
The meal in the conditioner is heated to temperature by steam. The heat of condensation in particular accelerates this process. The temperature initiates the starch gelatinization. This results in better digestion for pigs in particular and also produces glue, which can be compared with wallpaper glue. That is also a gelatinized starch product. We can use this glue to make a hard and especially durable pellet. The high temperature also ensures a better distribution of the water droplets.
3.3.3 Retention time
If we have brought moisture and temperature into a conditioner by steam, some retention time will result in kneadable and deformable particles. The larger the particles, the more time we need for moisture inclusion. The retention time in a conditioner is often very diverse. We see times between 8 and 180 seconds. In many cases the optimum will be somewhere around 40 to 60 seconds. With a view to capacity, we do not allow the particle a retention time of 180 seconds. At 8 seconds the moisture is on the outside of the particles. That is unfavourable when creating bonds.
3.3.4 Pressure and friction
In a process of pre-compaction (expansion, double pellet mill and BOA compactor) we use pressure and friction. This pressure and friction is created by the screw of the machine barrel, and by the mixing bolts in the barrel/screw, its conical shape and the use of an upper and lower pellet mill. The air is pressed out of the product, and it becomes less porous. Without air in the pellet, it becomes less brittle. The increasing starch gelatinization during this pressure process is very welcome for both digestion and pellet quality.
3.4 Pre-compactor
As mentioned before, there are 3 ways of pre-compacting:
- Expanding (Almex, Buhler)
- BOA compactor (Pelleting Technology Netherlands PTN)
- Double pellet mill (CPM, PTN, Van Aarsen, Buhler, DMT)
3.4.1 Expander
The product, warm and moist, will be pressed during transport through a conical worm in a barrel with mix bolts to a closable opening at the end. The more the opening closes, the greater the energy consumption, the higher the pressure and thus the temperature will increase (110 to 115⁰C). The starch gelatinizes more and more, resulting in better digestion (in swine) and better pellet quality. The use of an expander is very positive for pellet quality!
3.4.2 BOA compactor
This machine is a combination of a steam mixer and an expander. After a relatively small mixing chamber where steam is dosed, the product is pushed under pressure through an annular opening by means of rollers. This machine is also positive for the pellet quality.
3.4.3 double pellet mill
If there is sufficient installation height, a feed factory can opt for a double pellet mill system. After an upper press (larger pellet diameter), the hot and still kneadable pellet falls into a lower press with a smaller diameter. With a skilled operator, this system also brings better pellet quality.
3.5 pellet mill
A pellet mill forms the pellet. Without a pre-compactor, it uses a large amount of energy, the skilled craftsmanship of the operator plays a major role and the pelletability of the individual raw materials also has a certain influence on the pelleting result. With the use of a pre-compactor, less energy is used by the pellet mill. The skill of the operator is less important, and a greater diversity of resources can be used. The pellet mill contains a number of technical parts:
- die
- rollers
- meal scrapers
- knife
- roll distance
3.5.1 die
The die specifications play an important role in the production of a pellet with a certain hardness. The thicker the die, and therefore the pelleting path length, the more friction or resistance and the harder the pellet. The L/D ratio (length/diameter) says something about the resistance within the die. A pellet diameter of 3.5 mm and a pelleting hole length of 42 mm means an L/D ratio of 12. This is a friendly die. A pelleting hole length of 70 mm with this 3.5 mm pellet means an L/D ratio of 20. This results in more resistance and therefore a harder pellet. The choice of the most suitable die is essential for each animal group.
The wear pattern of a die is an underestimated topic. When a die wears normally, with a good adjustment of the meal scraper, most of the feed goes through the center part of the tread. When the die gets older, the most wear takes place in the middle part. If at certain moments, consciously or unconsciously, iron-on-iron is used with rollers and die, the outer rows will become over rolled and cause smaller holes. The pellets of the outer rows can then result in a higher hardness.
3.5.2 rollers
Some companies opt for groove rolls (with grooves), others opt for dimple rollers (with holes). Everyone has their own philosophy for their choice. Often based on the historic experience of previous operators. The dimple roller gives somewhat better quality, because the wear pattern occurs more evenly and can therefore also be used longer, also because the holes are deeper than the grooves on the groove roll are high. The groove roll is more often used for ‘heavy’ work and also in combination with the dimple roll on the left side in the die. The intention is that the meal is processed through the rolls on a 50/50 basis.
3.5.3 meal scrapers
The function of a meal scraper is to guide the meal to the tread surface of the die and a 50/50 distribution over both rollers. Sometimes the meal scraper is rigid and not adjustable. Then the supplier says that it is not necessary for the operator to adjust anything there. With an adjustable meal scraper, the skill of the operator is called upon. A skilled and committed operator is a positive factor for the final pellet quality!
With a commercial feed such as horse feed, a longer, tight pellet is greatly appreciated. This is not desirable for rabbits, broilers and piglets. Therefore, the operator is expected to adjust the knives in the press per animal group. In some factories, pellet length is even a parameter.
3.5.5 roll distance control
In the 1990s, roll distance control was introduced. With a few millimeters distance between rolls and die, a little increase in pellet hardness could be achieved. The slipping of the rollers could also be regulated with this.
3.6 Cooler
The final pellet hardness is achieved in the cooler. In this machine we remove the redundant moisture and cool the temperature back to ambient. Redundant moisture here refers to the moisture that is not used in the bindings. This process step has a considerable influence on the pellet quality. Often seen in feed mills is the poor product distribution in the cooler. With or without a spreader at the top, the product often moves resp. to the outside wall or in a heap in the middle of the cooler. After fifty years, we still can’t control this! The result is of course a considerable difference in the quality of bindings. Air chooses the path of least resistance and thus causes a significant difference in the cooling result!
In addition to parameters such as air volumes, air velocities and outside climate, retention time is an underestimated item in cooling. One of the visitors to Feed Design Lab gave me the following advice/explanation:
3mm pellet; needed cooling/retention time is 3×3=9 minutes
4mm pellet; required cooling/retention time is 4×4=16 minutes
5 mm pellet; required cooling/retention time is 5×5=25 minutes
This could be regarded as nonsense, but there is some of truth in this. In addition, the largest pellet diameters often contain a lot of crude fiber (sows/cattle) or a lot of molasses (cattle), which makes the cooling result more difficult.
3.7 sieve and crumbler
After cooling, a sieve installation (often from Mogensen) can remove a small amount of fines and dust back to the pelleting meal bin. However, if a lot is sieved here, more attention should be paid to conditioning and pelleting.
A crumbler will only make a good crumble if the pellet quality is adequate. A good crumble quality will never come from a moderate pellet.
3.8 coater
The purchase of a coater or vacuum coater brings many advantages.
o Post pelleting application: adding non-heat-resistant enzymes such as phytase
o Dustiness improvement
o Adding contaminating additives
o Several oil types can be used
o Use as a control parameter for pellet hardness
The latter is particularly interesting in this article. In the production of broiler feed and especially pig feed, the coater can be a control tool for pellet quality. There are known companies where the operator has the freedom to optimize the mixing-coating ratio with the addition of oil.
% oil | Hardness result | Next order | Hardness result | |
Mixing | 2,0 |
Pellet is too hard | 2,5% | meal is more savoury, less resistance in the die -> softer pellet |
Coating | 2,0 | 1,5% | ||
Total | 4,0 | 4,0% | ||
Mixing | 2,0 |
Pellet is too soft | 1,5% | Meal is dryer, more resistance in the die -> harder pellet |
Coating | 2,0 | 2,5% | ||
total | 4,0 | 4,0% |
Table 1: ratio oil mixing – oil coating and its result on pellet quality
Area 4: Steam
Where conditioning is by far the most important machine/process step to produce pellet quality, steam is by far the most important additive in this subject. As mentioned, we make good hard and durable pellets with a good amount of dry, saturated steam. This is made from water by a steam generator with an outgoing pressure of 7-9 bar. Due to the great distance to the conditioner, we lose some pressure, and a certain amount of steam condenses to condensation water. This water has a particularly negative effect on the pellet quality. The steam dosing set just before the conditioner has the purpose of reducing pressure, dewatering and controlling quantity. It often goes wrong, especially on the dewatering. Steam traps often get clogged without anyone in the factory recognizing it. There is a huge lack of knowledge of the steam dosing set, and it is often wrapped and isolated and hidden high behind a pellet mill. Moreover, this is extremely hot, so the advice: “don’t touch it!” Nowadays there are instruments, such as the QM1 from Armstrong, that test the effectiveness (read: dryness) of the steam dosing in real time and continuously. Indispensable in a well-equipped pelleting line! The operator or the PLC receives a signal when the quality of the steam becomes less and therefore wetter.
For consideration: do we continue dosing steam based on temperature or are we slowly switching to based on capacity? Many experts unanimously agree that capacitance-based dosing is much easier and better. What you only need for that is a known and measurable dry matter flow and a steam flow meter.

Source: an IVS dosing technology harness
Area 5: The Operator
An engaged operator with an inquiring mind will provide you with pellet quality. Some operators are not familiar with what actually happens inside the machine. Filling degree and retention time in a conditioner, steam quality testing, assessment of the air balance in a hammer mill or particle size assessment are subjects in which help can be needed. An experienced operator who, so to speak, listens, feels and smells how a pelleting process is performing does not really need measuring instruments. We have to train the operators in such a way that they feel like professionals!
Area 6: Miscellaneous
6.1 order-driven production
Where we used to produce for stock, it is now order-driven! This requires a different approach! 40 years ago, we used to be able to make adjustments with long production runs, nowadays we can’t do that with short runs. What we can do is make an adjustment within the next order of the same feed.
6.2 highly advanced software
Nowadays our customers order feed via the internet. This order is followed in a modern feed factory by a transport and production planning system that does not involve the use of human hands. The transport planning is leading, and the production planning adjusts accordingly. For example, it is possible that the feed is already delivered to the customer 15 minutes after leaving the cooler. Where in the past the product could ‘sweat out’ at the factory, this now happens at the customer, with all the nasty consequences that entails, such as condensation in the farmer’s silo.
6.3 silo effect
Pellet quality issues can also arise in the farmyard. If a farmer does not regularly empty and clean his silos, meal nests can form. So, then a small amount of feed remains in his silo. This last feed of the order always contains more fines than average due to the fact that pellets roll better than fines. The new, carefully produced good pellet is then poured onto it. If this happens often, this silo effect gets worse and worse. For an enlightening video of Borregaard, please contact Feed Design Lab.
6.4 in the farmyard
During the unloading of the pelleted products in the farmer’s silo, it is important that a bulk driver uses a lot of product and little air in the discharge line. The discharge pipe is at least 90 mm Ø. Product-on-product is deposited in the silo. Long discharge lines and many bends are not desirable. Weld seams or bad flange connections should also be avoided.
Pellet quality is not a skill you will learn on one afternoon! It is very important to learn from your own installation / process. You have to ‘make’ your process out of glass! Awareness on what’s happening in your own facility. How professional is my grinding knowledge? How professional is my experience on conditioning and do I have any idea how to judge my steam quality? There’s a lot of technique available in this world, how about technology? ………….
That’s my profession!
Eric Vissers
For any questions on this article, please contact Feed Design Lab in The Netherlands.